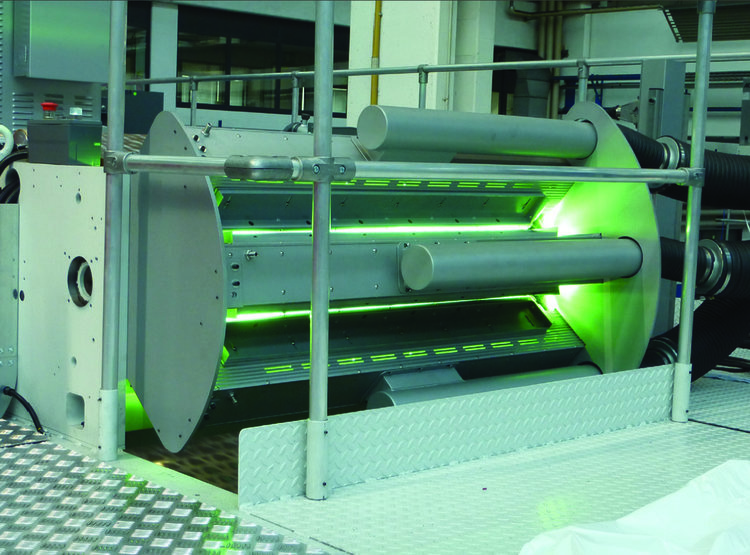
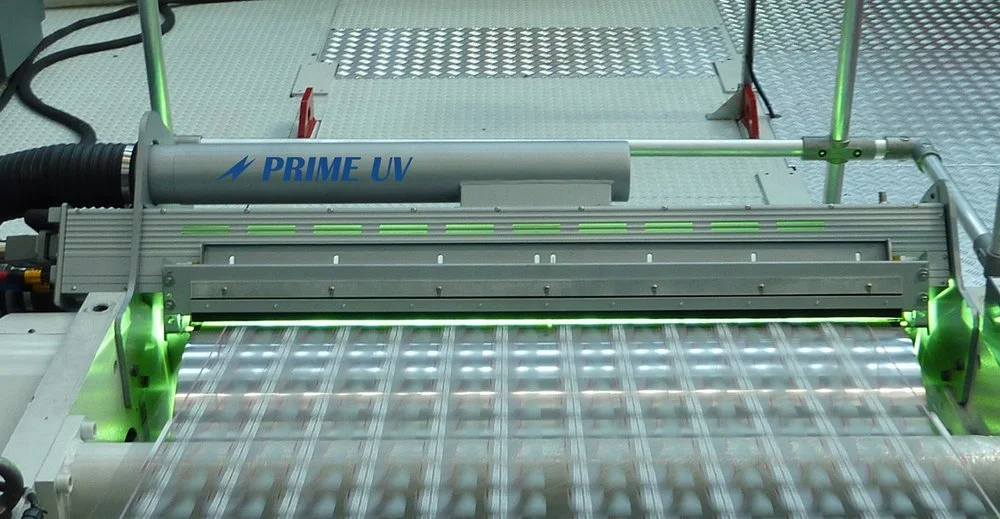
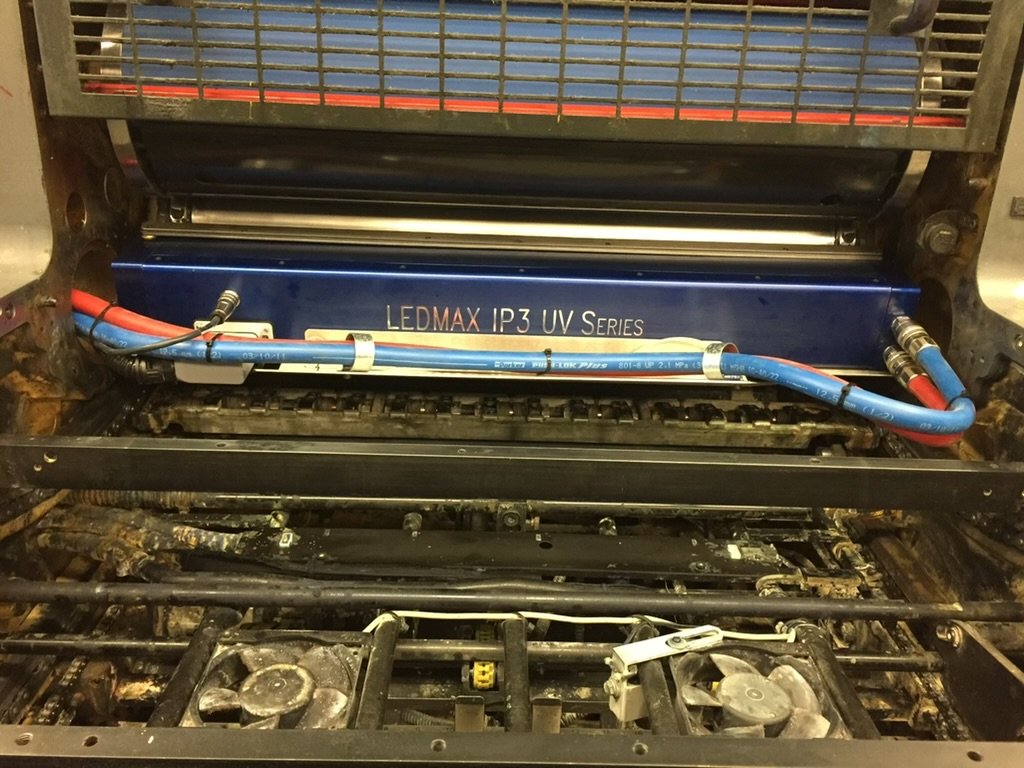
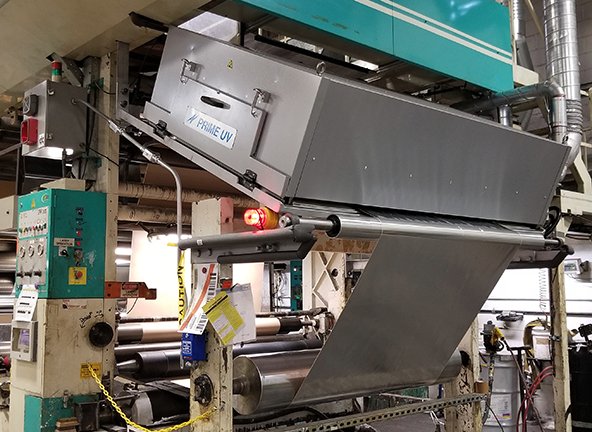
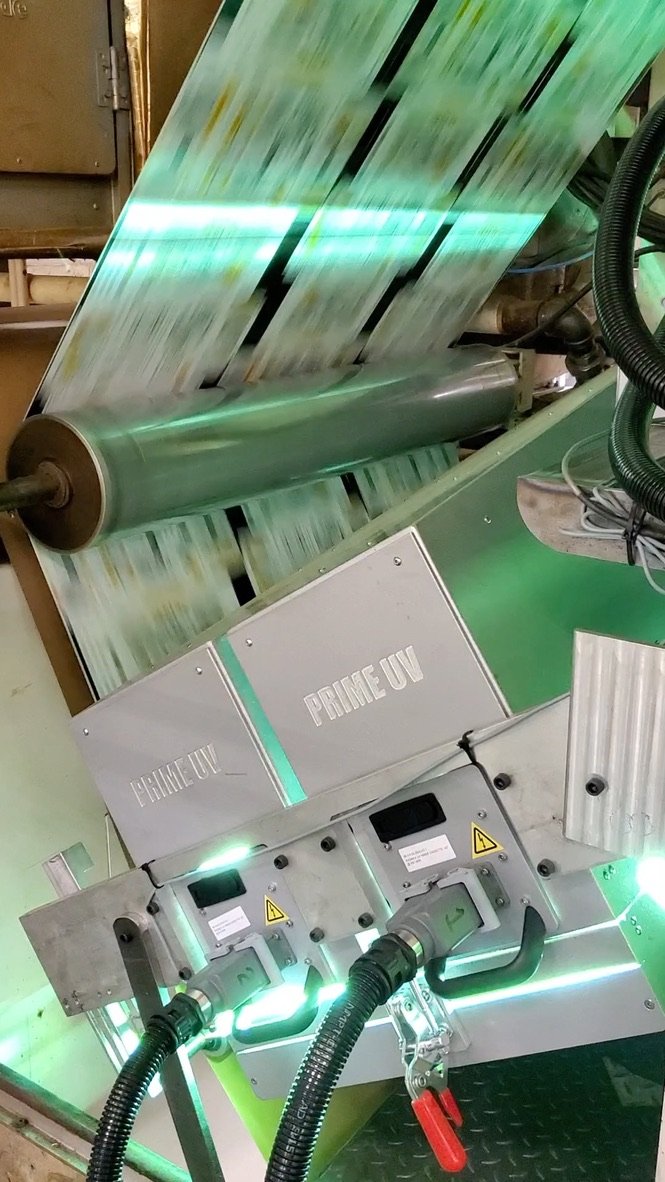
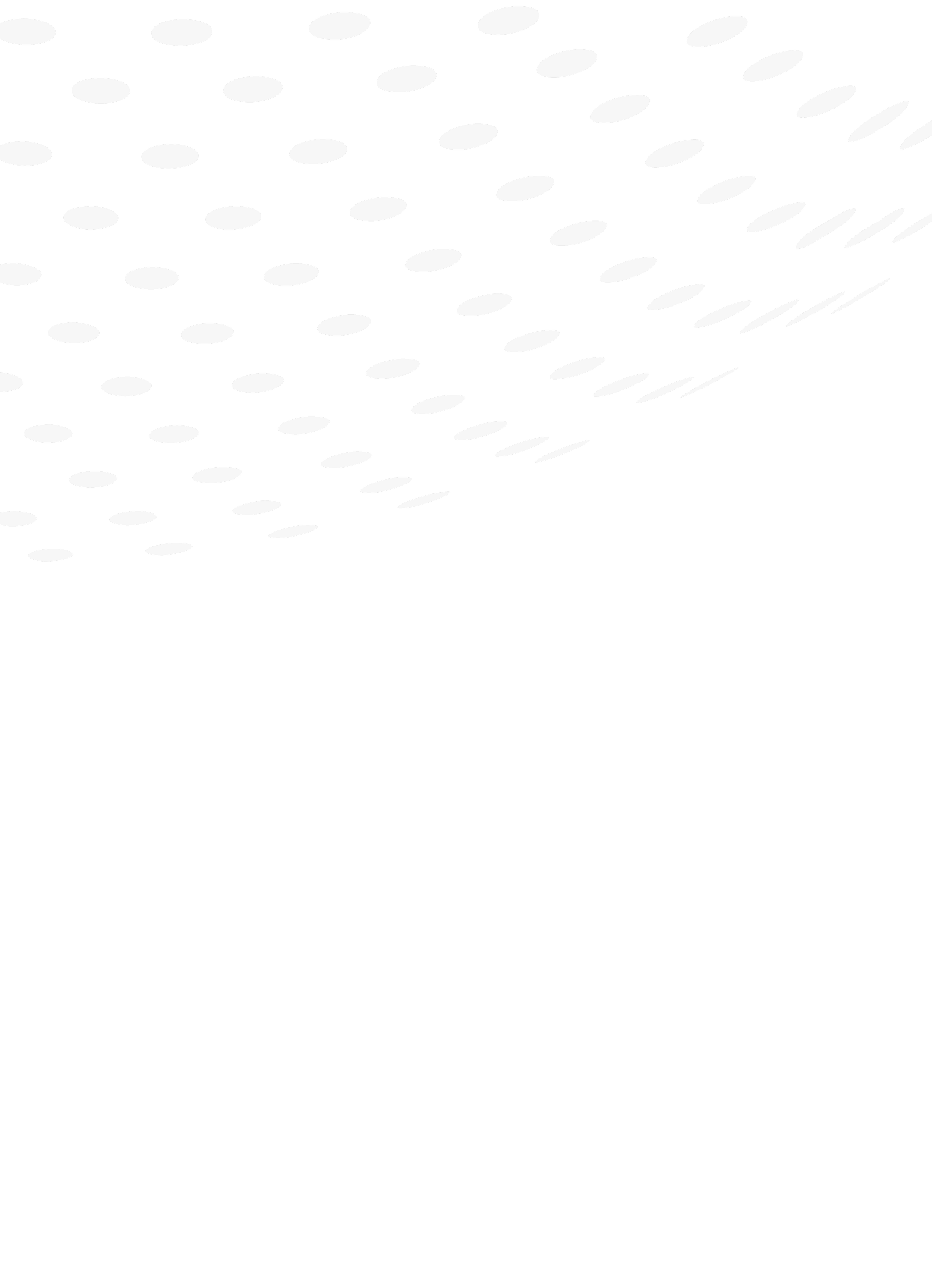
UV CURING
UV CURING - INTRODUCTION
UV curing refers to using Ultra-Violet (UV) energy to cure (dry) chemistry which is specifically formulated to cure (dry) when exposed to UV energy.
Most likely several times today you have handled an object “cured” using ultraviolet (UV) processing by simply lifting your morning cereal box, carrying a 12-pack of beer, reading a magazine, using your hotel key card, typing on your keyboard, driving your car or simply walking on your hardwood floor.
UV curing refers to a special way in which coatings, inks, adhesives, composites and other materials may be cured (dried), rather than traditional methods that typically use more energy and create harmful emissions. In effect, the ultraviolet light spectrum produced by a UV lamp interacts with specially formulated chemistries to cure materials–typically more quickly, using less energy and thereby at a lower cost than other drying methods.
The advantages of UV are well-documented–mainly when used with manufactured products that require fast processing and/or on substrates that are sensitive to heat. In addition, UV curing is considered environmentally responsible since most of the solvents in traditional processes may be eliminated, thanks to the special capabilities of UV curing.
UV Chemistry Basics
“DRYING” vs. “CURING”
In simplest terms, drying of an ink film occurs with conventional inks when the ink vehicle (solvent, oil) evaporates or is absorbed, leaving behind the solids (pigments, resins, waxes, dryers, etc.) to form a film on the substrate surface.
In radiation curing, on the other hand, all of the components in the ink or coating remain on the surface of the substrate, but are chemically transformed into a hard film through exposure to Ultra Violet lights (UV) or a concentrated beam of highly energized electrons (EB).
The difference lies in the chemistry of the materials in the inks and coatings, and in the pressroom equipment needed to “energize” the curing process.
Figure 1 (below) is a graphic illustration of the relationships of the various ingredients:
Figure 1
Rudimentary Ink Chemistry
UV curing is the term for the utilization of electromagnetic energy - principally in the 200-400 nanometer band (see Figure 2), to turn a fluid film into a solid. Another suitable description for this process is called cross linking (see next page, Figure3). The catalyst that causes this reaction is the photoinitiator. Once the substrate runs under the UV light source the curing is instantaneous, in a radical system what has not cured under the source will not cure unless it’s put under the source again.
Figure 2
Figure 3
The materials used in radiation curable ink formulas are considerably more “user friendly” today than ever before. Advancements in raw materials will continue to make radiation curable inks and coatings more commonplace in the years ahead. The major components of UV and EB inks are:
Reactive diluents (monomers)
Fluid resins (oligomers)
Photoinitiatiors (UV only)
Additives
Pigments
The jobs of each of these chemicals are as follows:
Reactive Diluent (monomer) - A reactive diluent monomer is a simple, lightweight chemical that is similar to a solvent in its ability to thin down the ink. Monomers determine the surface characteristics of the inks - such things as gloss, hardness and flexibility. Monomers with high draize values are also the chemicals that give uncured UV and EB inks their most hazardous characteristics.
Resin (oligomer) - The resin in radiation curable inks is actually called an „oligomer‟. As in conventional inks, the resin is the chemical backbone of the ink. Among others, it provides the body, wetting ability and binding properties of the ink.
Photoinitiators - In UV inks, the photoinitiator is the chemical that becomes „excited‟ and starts the curing reaction when exposed to ultraviolet light. The excited photoinitiator passes that energy to the other components. At that point, any component, which becomes excited, has the ability to attract other components to itself and transfer energy to the newly attracted component.
Photoinitiators are not required in EB inks. The highly charged energy of the electron beam is sufficient to activate polymerization.
Additives - Additives include waxes, wetting agents, and rheology modifiers. They provide the added customizing touches to the ink.
Pigments - Pigment particle size and concentration can affect the curing rate of a UV ink. Pigments are therefore selected not only for color but for their wettability or oil dilution ratio, and for their receptivity to UV light. Among process colors, yellow and magenta are the easiest to cure, followed by cyan and black. Because black tends to simply absorb the wavelengths of UV light, more energy is required to obtain a satisfactory cure.
Pigment selection is not as critical in EB inks since the energy level of the Electron Beam is sufficient to cure even heavy ink films, regardless of color.
Polymerization
Any component that is excited or energized is called a “free radical‟. It is the free radicals that have the energy to keep the curing or “polymerization” chain reaction going. Each chemical chain continues growing until one of two things happen:
■ The excited chains use up all of the available components, or
■ Some foreign substance, such as oxygen, „quenches‟ or halts the reaction.
THE UV CURING PROCESS
UV curing describes the use of ultraviolet (UV) energy to polymerize a combination of monomers and oligomers found in UV Chemistry onto a substrate. The UV material may be formulated into an ink, coating, adhesive or other product. The process is also known as radiation curing as UV is a radiant energy source. The energy sources for UV or visible light cure are typically medium-pressure mercury lamps, pulsed xenon lamps, and UV LEDs
THREE GREAT REASONS TO CONVERT TO UV TECHNOLOGY
-
Since most systems are solvent-free and require less than a second of exposure, the productivity gains can be tremendous compared to conventional coating techniques. Web line speeds of over 2,000 ft/min. (650 meters/minute) can be achieved and the product is immediately ready for testing and shipment.
-
Most systems do not contain any water or solvent. In addition, the process provides total control of the cure temperature making it ideal for application on heat-sensitive substrates.
-
UV Chemistry Compositions are typically solvent-free so emissions and flammability are not a concern. Light cure systems are compatible with almost all application techniques and require a minimum of space. UV lamps can usually be installed on existing production lines.
UV CURABLE CHEMISTRY
Content Source: Radtech.org
-
They are the simplest building blocks from which synthetic organic materials are made. A simple monomer derived from petroleum feed is ethylene. It is represented by: H2C=CH2. The symbol “=” between the two units or atoms of carbon represents a reactive site or, as chemists refer to it, a “double bond” or unsaturation. It is sites like these that are capable of reacting to form bigger or larger chemical materials called oligomers and polymers.
-
A polymer is a grouping of many (i.e. poly-) repeat units of the same monomer. The term oligomer is a special term used to designate those polymers which often can be further reacted to form a large combination of polymers. The unsaturation sites on oligomers and monomers alone will not undergo a reaction or crosslinking.
-
The overall properties of any coating, ink, adhesive or binder crosslinked by radiant energy are determined primarily by the oligomers used in the formulation. Oligomers are moderately low molecular weight polymers, most of which are based on the acrylation of different structures. The acrylation imparts the unsaturation or the “C=C” group to the ends of the oligomer.
-
Monomers are primarily used as diluents to lower the viscosity of the uncured material to facilitate application. They can be monofunctional, containing only one reactive group or unsaturation site, or multifunctional. This unsaturation allows them to react and become incorporated into the cured or finished material, rather than volatilizing into the atmosphere as is common with conventional coatings. Multifunctional monomers, because they contain two or more reactive sites, form links between oligomer molecules and other monomers in the formulation.
-
This ingredient absorbs UV energy and is responsible for the production of free radicals or actions. Free radicals or actions are high-energy species that induce crosslinking between the unsaturation sites of monomers, oligomers and polymers.
-
The most common are stabilizers, which prevent gelation in storage and premature curing due to low levels of light exposure. Color pigments, dyes, defoamers, adhesion promoters, flatting agents, wetting agents and slip aids are examples of other additives.
Recommended prime products for this TECHNOLOGY
Get in Touch with a Product and Application Specialist
Contact us to learn how Prime UV-IR’s curing and drying solutions can improve your production process, reduce your energy consumption and expand your product offerings.