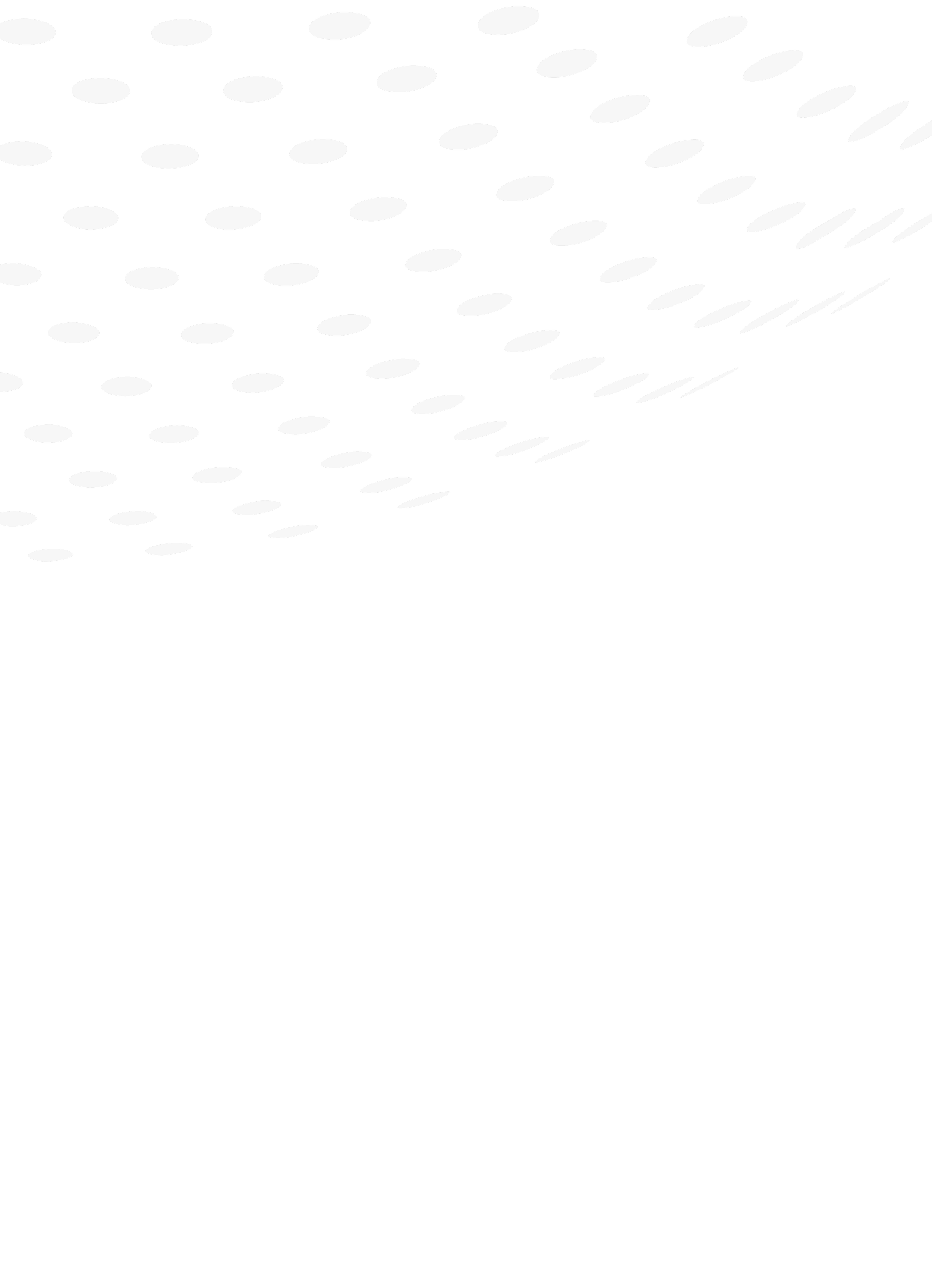
NITROGEN INERTED UV CURING SYSTEMS
Oxygen often inhibits UV curing during the polymerization process. Curing certain UV formulations in a nitrogen inerted curing chamber enables these UV formulations to work on a wide variety of substrates very effectively and efficiently.
All Nitrogen Inerted UV Curing Systems, regardless of the end use application, share the below fundamental design criteria:
UV Curing Chamber provides curing area inerted with Nitrogen to displace Oxygen.
Properly designed Distribution network to efficiently displace the Oxygen.
Nitrogen Gas.
High Performance material & component selection to ensure maximum UV Curing efficiency and peak performance of Nitrogen Inerted UV Curing Chamber.
Monitoring Controls & Nitrogen Distribution – ensure the efficient use of Nitrogen.
Oxygen Analyzers - Instrumentation to accurately monitor the Oxygen level within the Nitrogen Inerted UV Curing chamber.
Below more detail is provided about each of these necessary components.
-
The main function of this Curing chamber is to provide a UV Cure zone that has very effectively displaced the Oxygen and maintains oxygen at the lowest levels possible to provide the highest efficiency cure at various operating speeds for a variety of substrate types.
UV Chamber designs incorporate Nitrogen recovery.
A quartz window is used to allow the transmission of UV radiation into the chamber.
-
Nitrogen introduced into the Inerted Chamber needs to be diffused quickly and efficiently in the UV cure zone. A properly designed system will help maintain a homogenous concentration of Nitrogen throughout the chamber.
Once the Nitrogen is distributed, retaining the gas is necessary to maintain efficiencies of the system.
The use of an air knife is an efficient way to limit the leakage of Nitrogen from the chamber.
-
Many grades of nitrogen gas exist. Inerting a chamber to any level is only as good as the grade of Nitrogen gas used. Utilizing a high quality nitrogen source with a low level of Oxygen is critical. Industrial Nitrogen is commonly used in Nitrogen Inerted Chambers.
Nitrogen purity is generally expressed as a percent, such as 99% Nitrogen (which means 1% Oxygen with the balance of nitrogen and other inert gases.)
Inerted Chambers which require a low volume of nitrogen use often use a bottled Nitrogen supply.
If the Inerted Chambers require a high volume of nitrogen use, then an on-site nitrogen generator is typically installed.
-
One such critical component is the choice of quartz used as the transmission window located within the Inerted Chamber. What materials and methods are used to seal around this window are also important.
Natural Fused Quartz vs. Synthetic Quartz: The use of synthetic quartz is increasing due to the improved transmission of energy throughout the entire UV spectrum.
Other materials & components which are given much consideration include the following;
UV Bulbs type and design.
UV Power Drivers.
Air Knife design, mounting and adjustment design.
Compression seals
Chamber’s internal cooling method and type.
Chamber design to allow for internal access on larger, higher speed Inerted Chamber applications.
-
The Nitrogen Inerted Curing Chamber must accurately control the volume of nitrogen being fed into the Curing Chamber as the substrate both pulls oxygen into the system and pulls nitrogen out of the system. The Curing Chamber must automatically be kept with a constant level of nitrogen to ensure the proper cure of the UV chemistry being used. Typically oxygen levels must be kept under 50ppm. Critical to the performance of a Nitrogen Inerted Chamber is the following:
Number and location of Nitrogen feed control valves (ports.)
Type and accuracy of these control valves.
Software Interface of nitrogen supply valves into the Nitrogen Inerted Chamber coupled with Oxygen analyzer sensors.
Utilization of quality PLC and sophisticated software coding to ensure Inerted Chamber meets performance specifications.
-
The use of a high quality oxygen analyzer is critical for the successful performance of a Nitrogen Inerted UV Curing Chamber. The oxygen analyzer must not only be accurate but it must process the oxygen content very quickly. Nitrogen Inerted Curing Chambers utilized in high volume production applications use closed loop systems where Nitrogen is automatically delivered into the system based upon the oxygen content shown. Other important criteria include:
Placement and number of oxygen level monitoring sensors within each zone of the Inerted Chamber.
There are a number of available Oxygen analyzers. Choosing the best one for the specific application is critical
Get in Touch with a Product and Application Specialist
Contact us to learn how Prime UV-IR’s curing and drying solutions can improve your production process, reduce your energy consumption and expand your product offerings.